Adapting Grain Management Strategies to Meet a Changing World: Insights from CESCO CEO
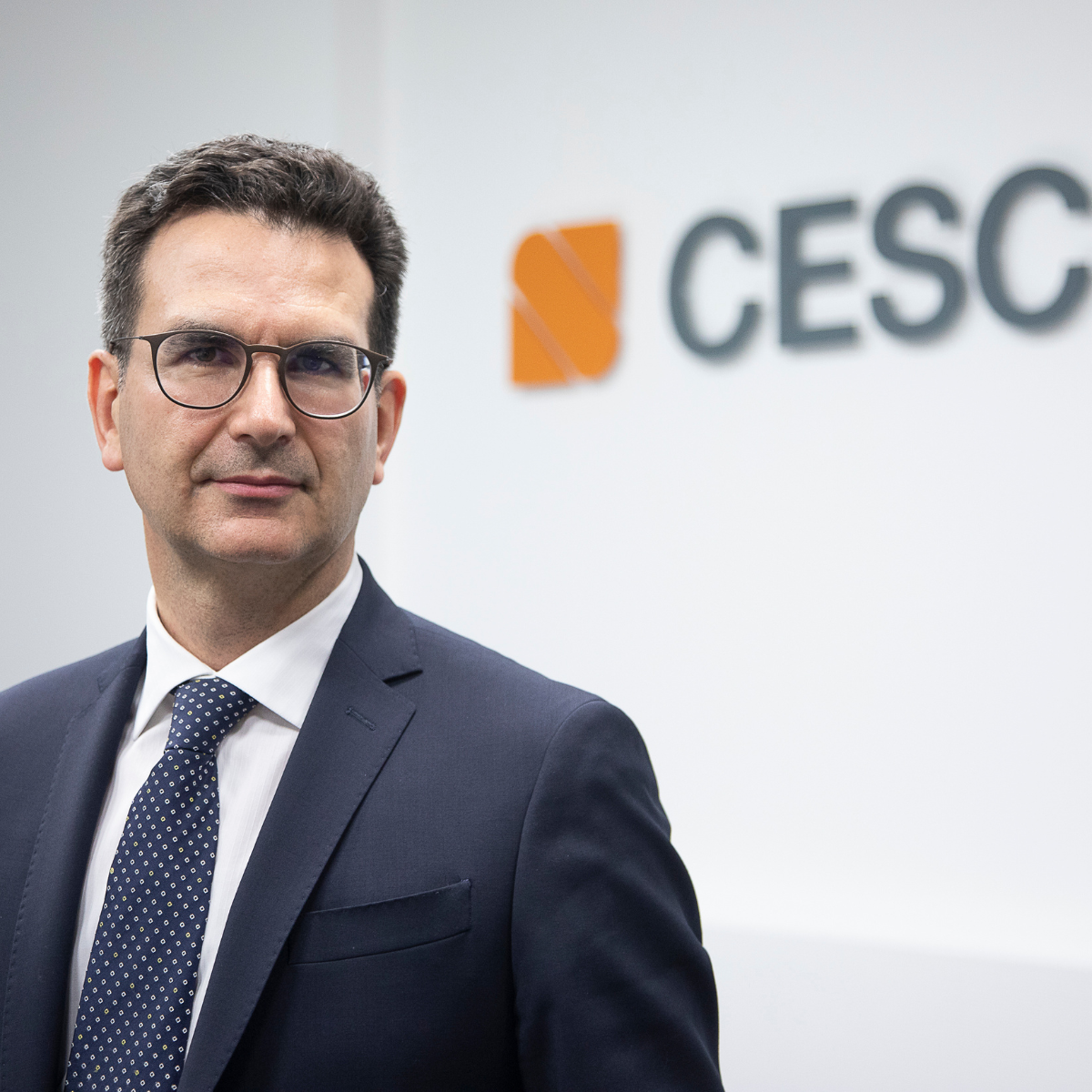
We are excited to share an insightful interview featured in Miller Magazine with Dr. Martino Celeghini, CESCO CEO. We would like to extend our gratitude to Miller Magazine for this opportunity to discuss the innovative strategies and resilience that define CESCO in today’s rapidly evolving grain management landscape.
In an industry where innovation meets necessity, CESCO EPC GmbH stands out as a model of invention and resilience. At the helm of this pioneering company is Dr. Martino Celeghini, a forward-thinkingindustry leader At the helm of this pioneering company is Dr. Martino Celeghini, a forward-thinking industry leader contributing to the future of grain storage and logistics. In our recent conversation, Dr. Celeghini explained how CESCO manages the many complexities of modern grain logistics, combining cutting-edge technology with decades of experience to meet the growing demands of the industry. “We are constantly innovating to address the major trends and challenges in grain logistics,” Dr. Celeghini explained. “From increasing storage capacities to ensuring environmental sustainability, our goal is to provide smart concepts and easy operation solutions.”
Addressing environmental concerns and responding to global unpredictability, CESCO’s strategic innovations are establishing new benchmarks in grain storage. Here’s an inside look at our discussions, revealing the insights and proactive approaches that keep CESCO at the forefront of the industry.
What are the current trends in grain logistics, and how is CESCO incorporating these trends into its projects and solutions?
a. Bigger, Faster, Unstoppable, Environmental-friendly:
i. A major trend is the increase in total storage capacity, ranging from 100 to 300 thousand tons, with some requests reaching 500 thousand tons. CESCO addresses this trend in cooperation with its partner for corrugated steel sheet silos, Simeza, offering large flat-bottom silos with diameters up to 32.10 meters, heights up to 37.90 meters, and single capacities up to 20,000 tons each.
ii. The silos are combined with high-capacity heavy-duty conveying equipment capable of handling up to 1200 or even 1500 tons per hour. To meet these demands, CESCO has developed a new line of heavy-duty chain conveyors, bucket elevators, and belt conveyors, drawing on over 50 years of market experience. CESCO’s new designs feature heavy-duty pillow block units for bearing supports installed externally, allowing complete replacement from outside. All stations have rounded shapes to enhance product hygiene, with internal walls lined with HDPE or Hardox liners to reduce wear. The gearboxes are installed with taper bush fittings to prevent pitting and ensure long-term maintainability. Additionally, CESCO applies a dual-motor solution when the machine requires an installed power greater than or equal to 37 kW. These motors are controlled by the control panel to operate in parallel and simultaneously, ensuring better distribution of both the motor’s weight and the required stresses on the shaft. This dual-motor solution also allows the conveyor to run at 50% capacity in the event of a problem with one of the motors.
iii. The equipment is fitted in the plant with a high degree of redundancy to ensure uninterrupted operation during maintenance, avoiding single points of failure. CESCO addresses this need by thoroughly discussing customer requirements and optimizing plant design at the concept level, embodying the motto “smart concepts, easy operation.” Only after extensive concept optimization is the project fully engineered.
iv. Environmental aspects, such as reducing dust emissions and noise, and lowering energy consumption, are increasingly important in the grain business, pushing for fully enclosed belt conveyors to replace traditional chain conveyors. CESCO has developed a new line of heavy-duty, fully enclosed belt conveyors, Series RBC E, with conveying capacities up to 1200 tons per hour.
b. FSWH:
i. Several customers are also requesting storage systems based on flat storage warehouses (FSWH), especially for non-flowing materials.
ii. CESCO has developed a dedicated line of chain and belt conveyors with movable outlets on the top and grating inlets on the floor, ensuring uniform filling and emptying of the warehouse.
iii. CESCO is developing several projects combining round and square silos with flat storage warehouses according to customer demand.
What are the biggest challenges you foresee for the grain logistics in the next decade?
BE PREPARED FOR THE UNFORESEEN
While the challenges in the last decades were primarily driven by technological and economic improvements, since 2020, new factors like pandemics, wars, and economic embargos have heavily influenced grain logistics in unexpected ways.
The business must adapt to such unforeseen events quickly and flexibly. Regardless of the plans prepared, the only reliable way to ensure food security is by increasing local production or, if not possible, increasing strategic storage as seen in the trend mentioned above.
REFURBISHMENT AND EXTENSION OF OLD PLANTS
Several plants worldwide are aging and require upgrades, particularly in conveying systems, control systems, and increased storage capacity. To cope with this demand, CESCO has developed a methodology involving 3D digital imaging by laser scanner of existing facilities at the project’s beginning, paired with 3D full CAD design, ensuring accuracy and ease of assembly.
When plant expansion is required in limited space, often the case for mill plants, CESCO offers a variety of square silos with corrugated or flat smooth walls, seamlessly integrated with supporting steel structures. This allows for higher efficiency of space usage, reduced transport costs, and faster erection due to a fully bolted design.
TIME TO DELIVERY
Customers are demanding faster deliveries of plants and equipment due to urgent demands or changing conditions (e.g., supply chain disruptions, wars, embargos). CESCO has addressed this by developing a modular design for equipment and plants, fully implemented in 3D CAD and PDM/ERP systems and partnering with internal and external manufacturers for fully automated steel sheet component and warm rolled profiles production, reducing design and manufacturing time.
Additionally, the wide network of manufacturing facilities within the CESCO group ensures that the project scope is spread across a broad base of suppliers, removing bottlenecks while meticulously managing and tracking production lots from drawing release to delivery and erection on site.
ENVIRONMENTAL CHALLENGES
Temperature rise: Global warming leads to higher temperatures, which can become critical for safe grain storage. Ventilation and recirculation may become less effective with high temperatures and humidity. New cooling technologies are necessary.
Heavy rainfalls and humidity: The large masses of water stored in clouds cause tropical rainfalls in regions and seasons not typically affected by this weather. We have observed flooding across Europe and even in Dubai this year. CESCO has long experience in designing plants and steel structures to withstand heavy rainfalls and shallow soil water levels, ensuring long-term operation even in adverse weather. Corrosion issues are addressed by using galvanized steel sheets and hot dip galvanized warm rolled profiles with high zinc coatings up to Z900 grade.
No chemicals: Fumigation is becoming more and more challenging due to legislative restrictions and changing customer demands. New technologies, mainly using heat treatment, require plant design and silo design adaptations. CESCO has developed a strategy with few hospitalization silos fitted with heat treatment equipment. Steel mill buildings with sandwich panel insulation are optimal for economical heat treatment.
How does CESCO ensure the efficiency and reliability of the grain supply chain from storage to processing? What strategies are employed to minimize losses and maintain grain quality?
Safe storage through;
i. Ventilation
ii. Recirculation
iii. Pellet fumigation or heat treatment
iv. Avoidance of product accumulation
v. Temperature monitoring
vi. Visual inspections
Reliability of grain supply chain by;
i. High reliability of each conveying equipment (heavy-duty type)
ii. Redundancy of equipment within the plant (smart concept)
How do regional differences, such as climate and infrastructure, affect the design and operation of grain logistics and processing facilities?
Regional climate (temperature, humidity, rainfalls, wind loads, snow/sand loads) and geological characteristics (deep water level, seismic loads) greatly impact project design and need to be thoroughly assessed at the project’s start.
Generally, hot climate areas are negatively affected by drought and hotter, more humid climates, necessitating adaptations in plant and equipment for heat insulation, product cooling/ventilation, water drainage, and corrosion prevention.
Colder Nordic climate areas benefit from longer growing seasons with higher crop yields, demanding new storage and logistics facilities.
Both cargo ship and railway transport are becoming increasingly relevant, paired with traditional truck transport.
CESCO is known for its tailor-made plant designs. Can you describe the process of customizing a plant to meet a client’s specific needs in the grain logistics and processing sector?
CESCO begins by understanding the client’s needs in detail. Often, a request for specific equipment leads to a collaborative effort where the customer recognizes the value of an experienced partner, enhancing the concept together for long-term investment value.
Once the concept is created, basic and detailed engineering of the plant is performed with continuous information exchange using 3D CAD visualization, progressing from basic design to detailed design and manufacturing release.
Manufacturing and delivery of all components in several lots must be managed according to the erection plan. This requires clarity on transport and customs procedures and inspection of goods before or after delivery.
Once the material is delivered, on-site internal logistics must ensure proper storage and identification of different components.
Pre-assembly of bolted equipment and erection is typically performed by an assembly company under the direction and supervision of CESCO experts.
Finally, commissioning, load testing, and training are conducted with the customer’s team to hand over the plant.
How is digitalization transforming the grain processing industry? What digital tools does CESCO use to enhance its operations?
CESCO has fully embraced digital project execution and business management:
All engineering and commercial documents are created, processed, and archived digitally.
All internal and external communication is digital, still prioritizing face-to-face bilateral on-demand communication.
All CAD models, drawings, and manufacturing equipment are digital and numerically controlled, eliminating human errors in communication and execution.
Are there any upcoming projects or new technologies that you are particularly excited about? Can you share some details about any innovative projects or developments that CESCO is currently working on?
We are particularly excited about a project for the customer SCTB in Cameroon, involving a 20,000-ton storage silo and a flour mill building with round and square silos for raw material and finished products.
We are also completing the refurbishment of a 150,000-ton silo storage plant in the Alexandria Port in Egypt, with 2x640t/h belt conveyors. Further large projects are expected in Egypt in the near future.
We have signed a contract for a 200,000-ton silo storage facility in Saudi Arabia, to be delivered by the end of the year.
What are CESCO’s plans for future growth? Which markets do you see as having the most growth potential for company?
The Middle East is an interesting market with significant potential for new, innovative plants. Russia and Ukraine, currently halted markets, will become highly relevant once the geopolitical situation is resolved and rebuilding of damaged facilities is required, with restrictions lifted.
Are there any new collaborations or partnerships that CESCO is pursuing to enhance its market position?
CESCO has started a strategic partnership with the Swedish Company Tornum, recognizing mutual benefits in collaborating across different business areas. This collaboration continues to be beneficial.
CESCO maintains historical partnerships with German suppliers for motors, sensors, and bearing components, and with German and Italian suppliers for steel metal components, reinforcing our commitment to European design and quality.
Is there anything else you want to add?
Thanks for your interest in CESCO.